Technology
Let the light work for you
Clean and green disassembly of photovoltaic modules in a matter of seconds? This is possible at FLAXRES!
We have developed a technology that separates solar panels (and other composite materials) into their main components. The challenging part of recycling is the separation of the laminated polymer and solar cell composite. In our large-scale flashing unit FLAXTHOR®, the solar module is exposed to a very short, high-intensity light pulse for delamination.
Photovoltaic module before and after flashing
Our process begins with end-of-life modules. It doesn’t matter whether the front glass is intact or broken. The light travels through the transparent glass and polymer layer and is then converted into thermal energy by the light-absorbing layer (e.g. silicon wafer). The photovoltaic cells heat up in less than a small fraction of one second. Thermal treatment of the boundary layers results in the separation of the material. With the help of preceding and subsequent process steps, the photovoltaic module is separated into glass, aluminum, polymers, silicon with silver, junction box with cable and bus bars.
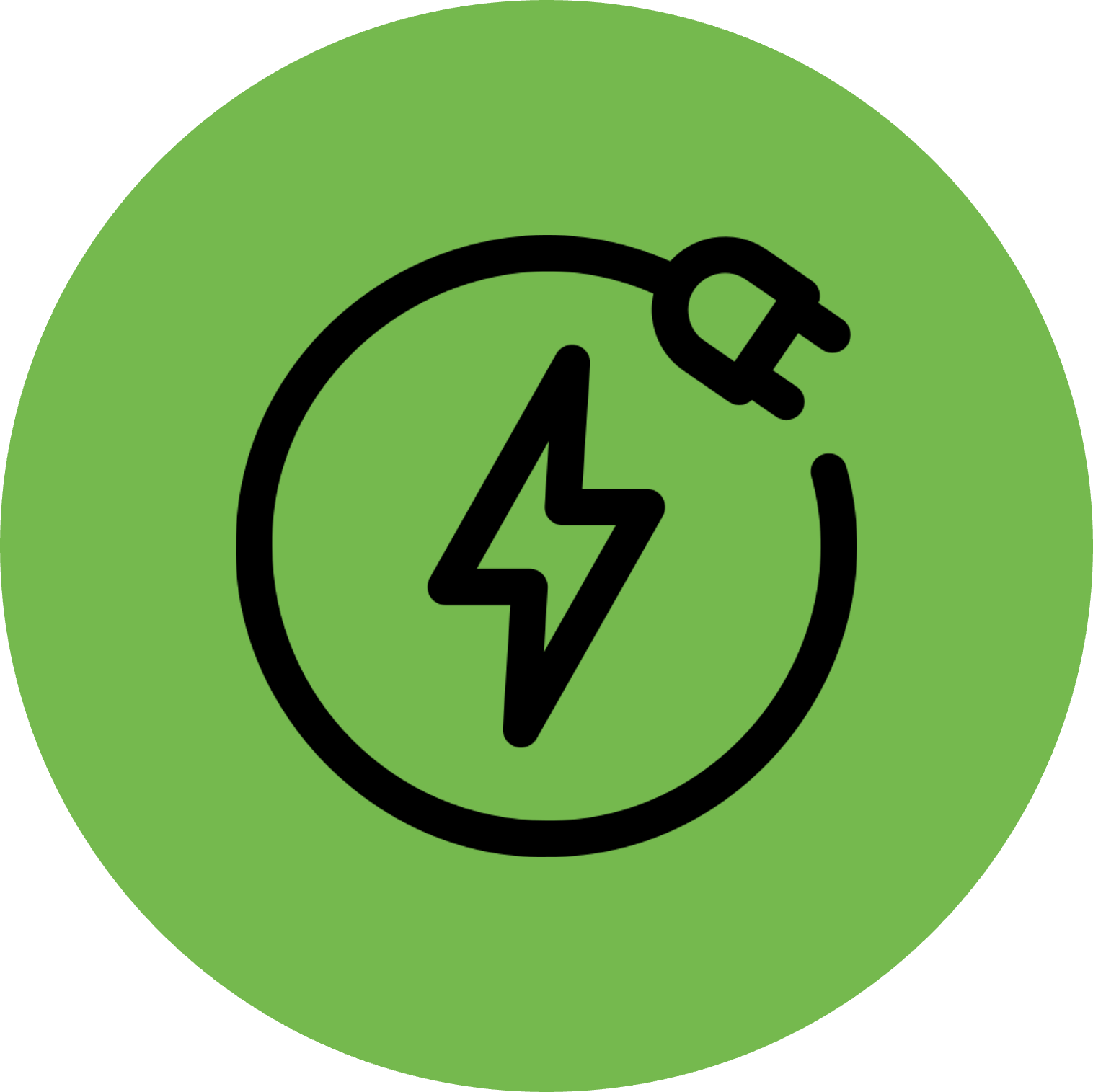
Preparation
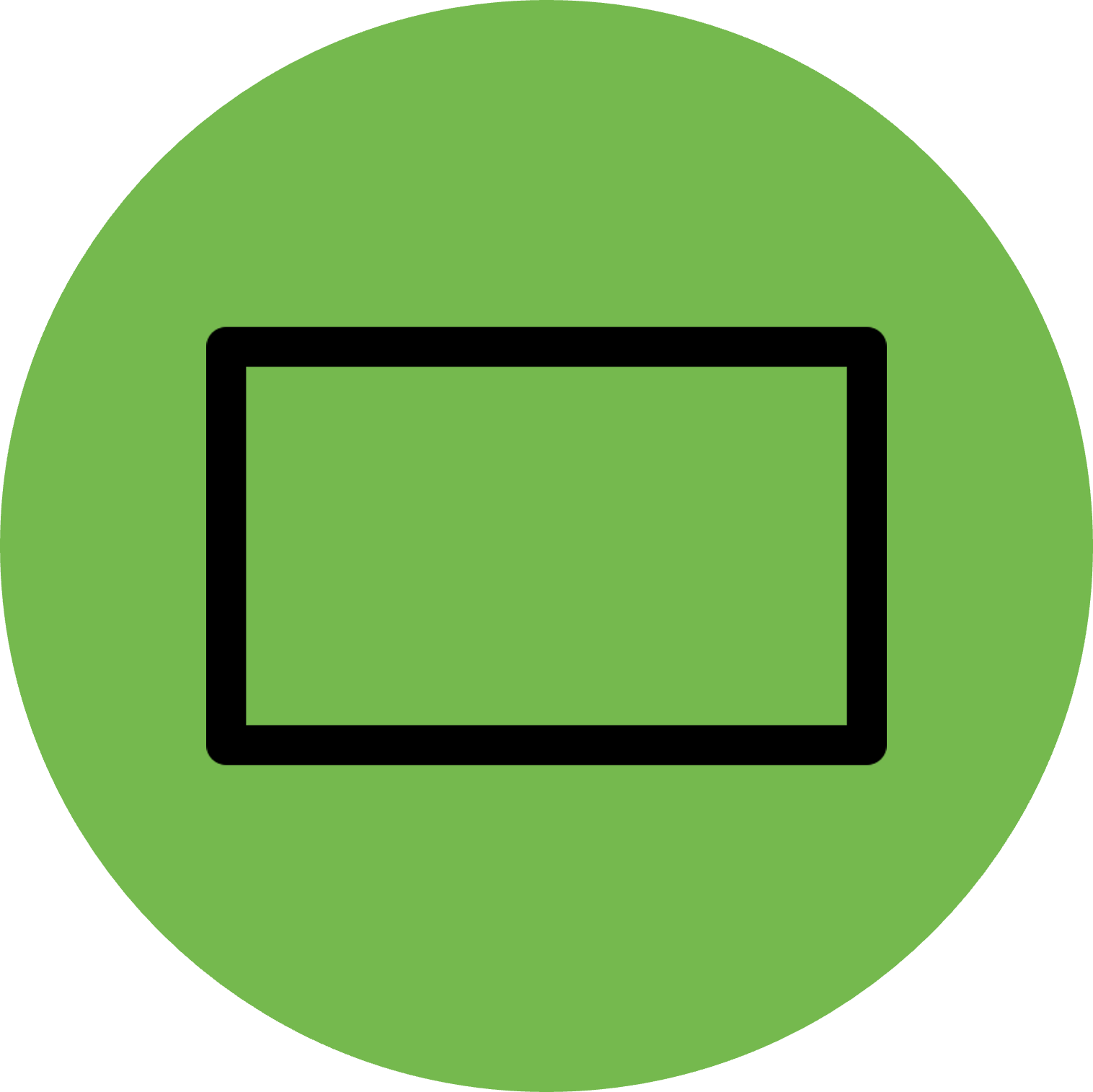
Deframing
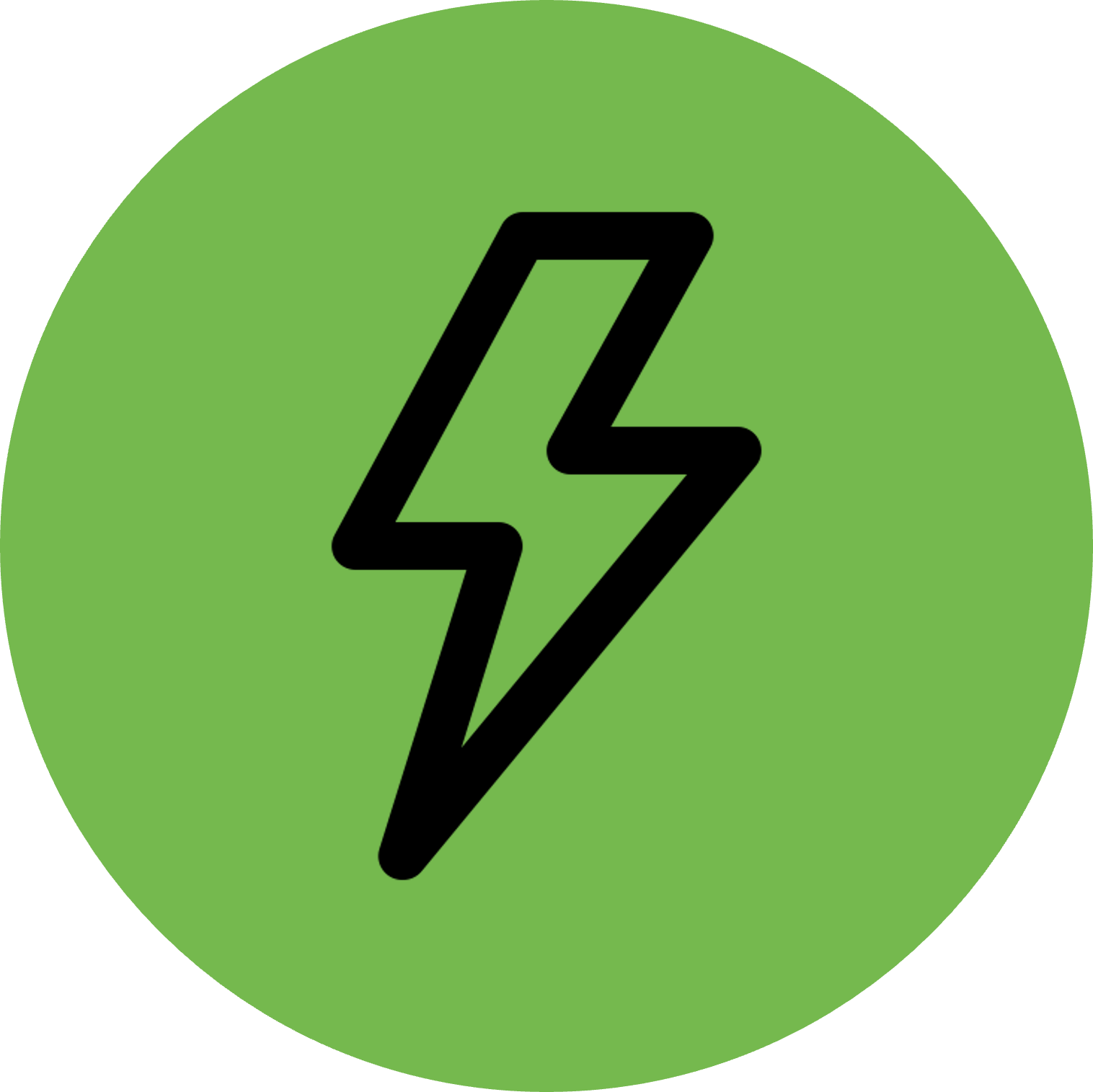
Flashing
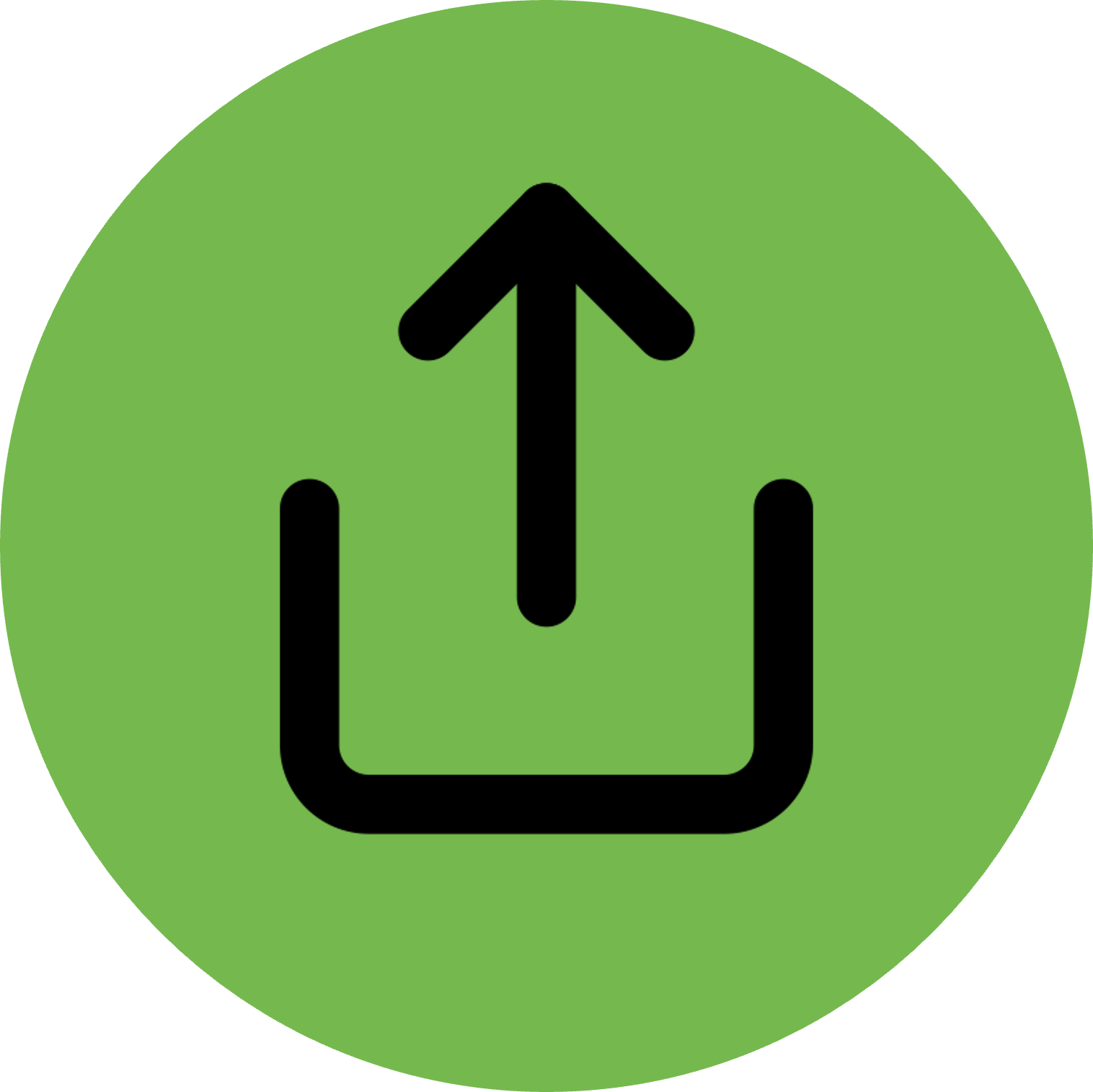
Extraction
Silicon
Silicon is probably the most important component of a wafer-based photovoltaic module. This is where the conversion of solar energy into electrical energy takes place. Utilizing our flashlight technology the surrounding polymer can be removed from the silicon wafer without leaving any residue. The recovery of a high purity wafer fraction is the centerpiece of our technology. It provides economical and ecological recycling for example the recovery of silver.
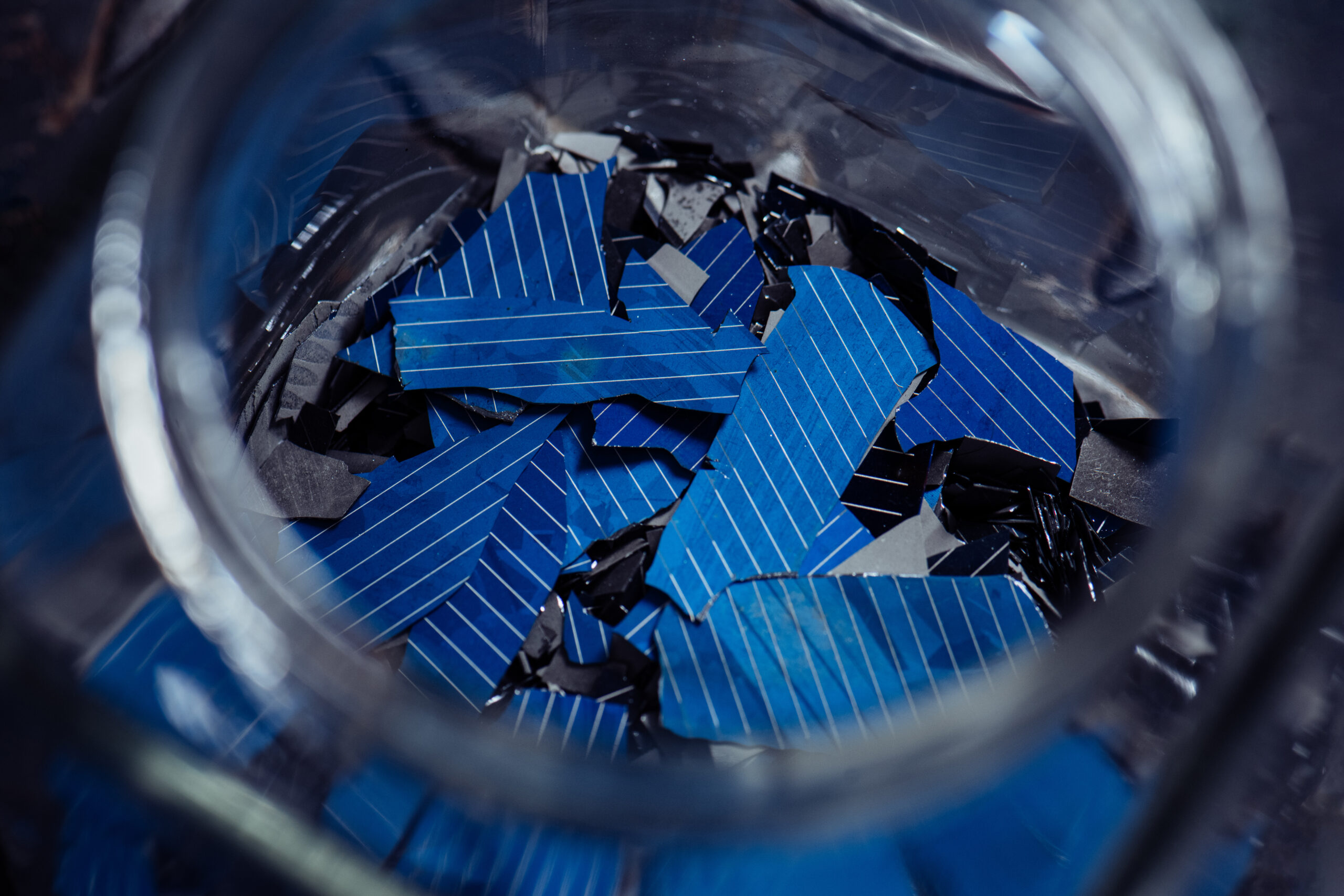
Thin-film layer
In terms of numbers, thin-film solar modules (e.g. with CdTe, CIS, CIGS or organic cells) do not dominate the market, but we consider the recycling of these modules to be important and worthwhile as well. Most of these types contain substances that are toxic to humans and the environment, for example cadmium. The disposal in landfills or uncontrolled sales to third parties would be a danger to everyone. With our recycling process, we can extract the light-absorbing layer, whether toxic or not. The recovered materials can be treated for reuse. In this way, rare materials like indium or tellurium remain in the cycle – for a sustainable economy.
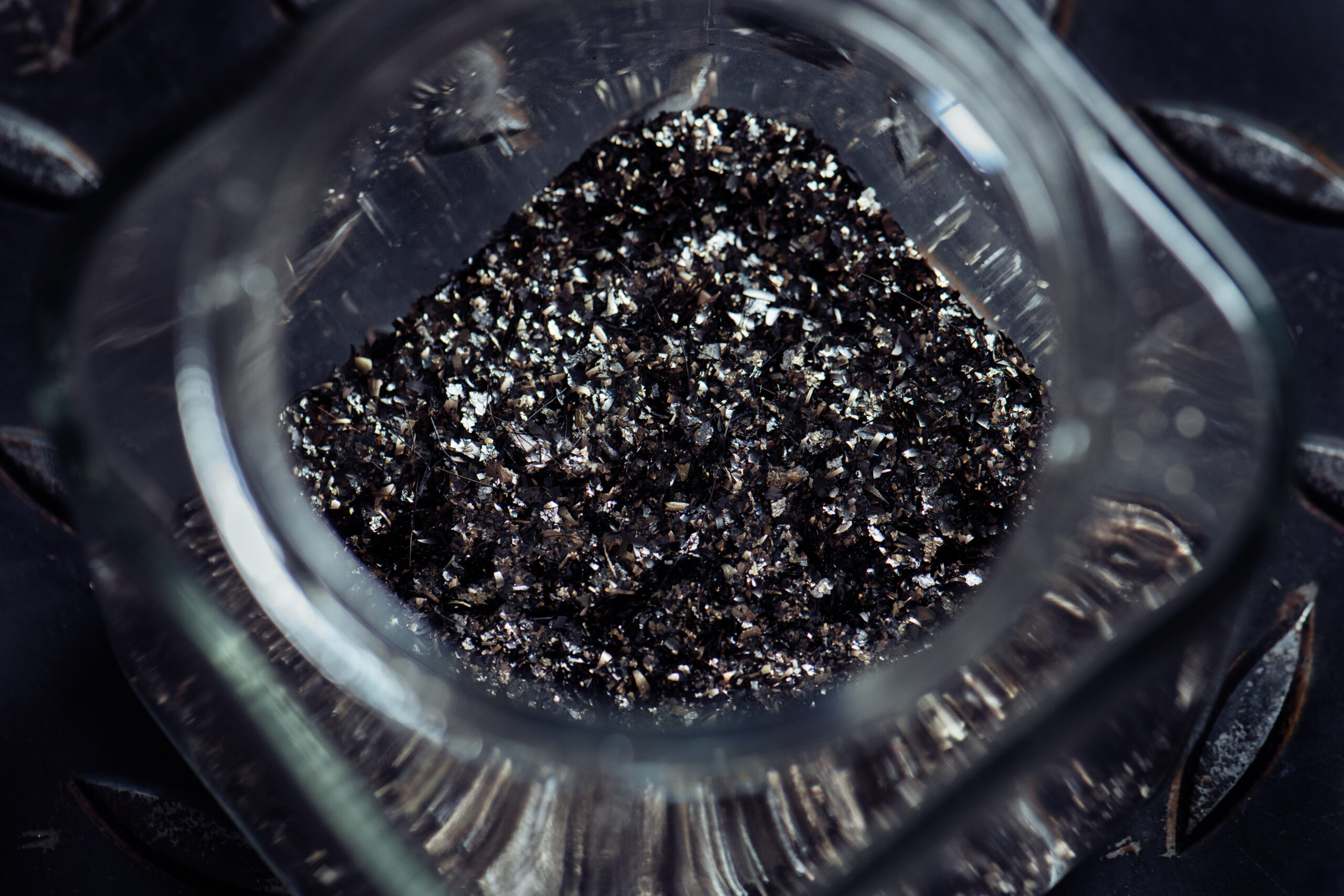
Glass
At around 70%, glass accounts for the largest proportion of weight in a photovoltaic module. The production of the low-iron solar glass is an energy-intensive process. It is, therefore, important to recover the glass fraction of the highest quality and return it to the material cycle. If a module with a broken front glass pane is processed, even the smallest contamination could lead to the discard in the glass manufacturing process. For this reason we pay particular attention to the process of glass recovery.
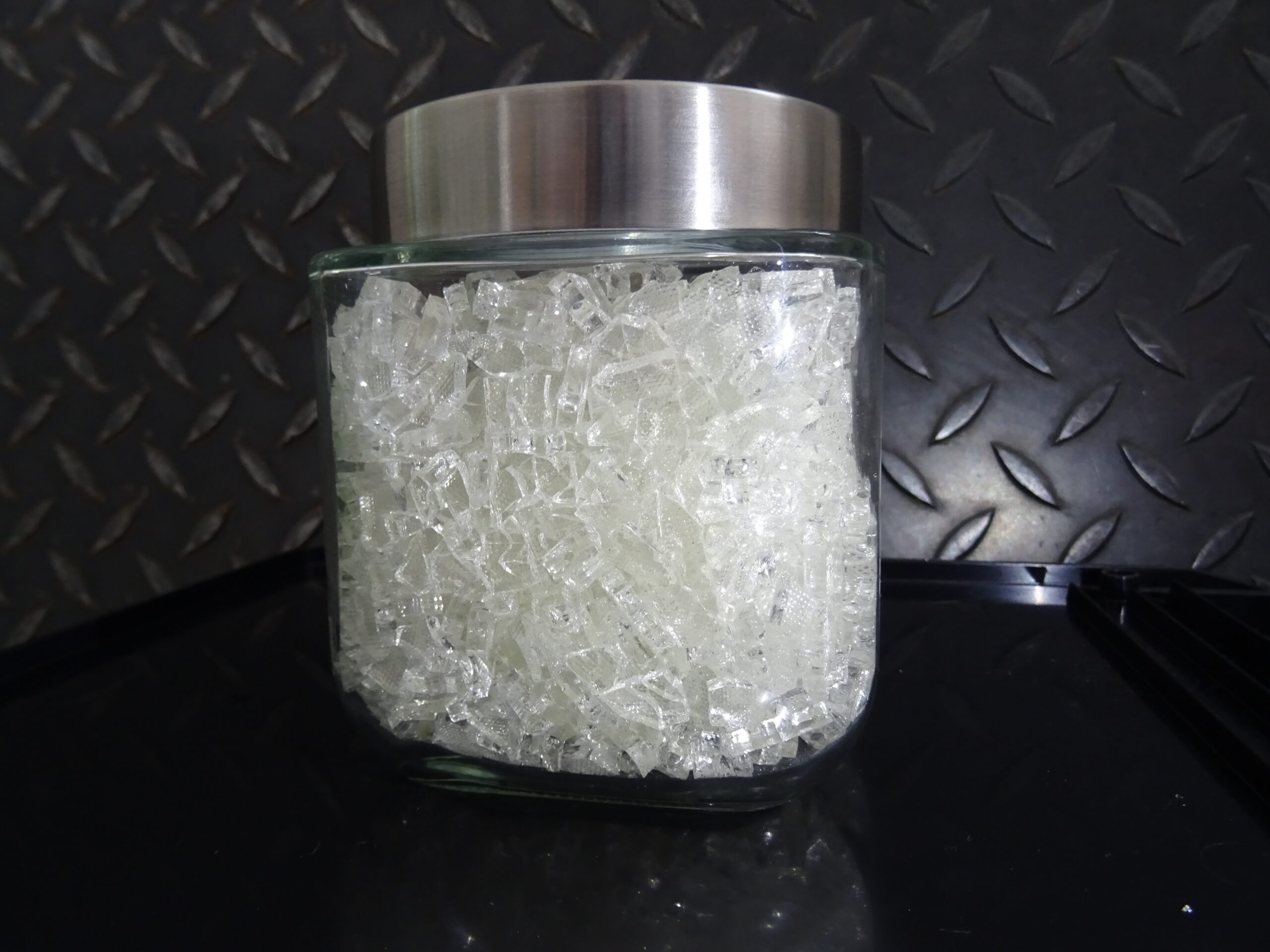
Mobile and worldwide
We stand for maximum efficiency and flexibility. Thanks to our mobile technology, which is built into oversea containers, it is possible to deploy our equipment as required. This allows us to directly approach the huge solar fields installed in countries like China, USA or India. The dismantling is carried out on site and each fraction, such as the heavy glass, can be transported to the raw material manufacturer without a detour to a recycling facility. The FLAXRES technology provides significant cost and CO2 reductions by minimizing transportation.
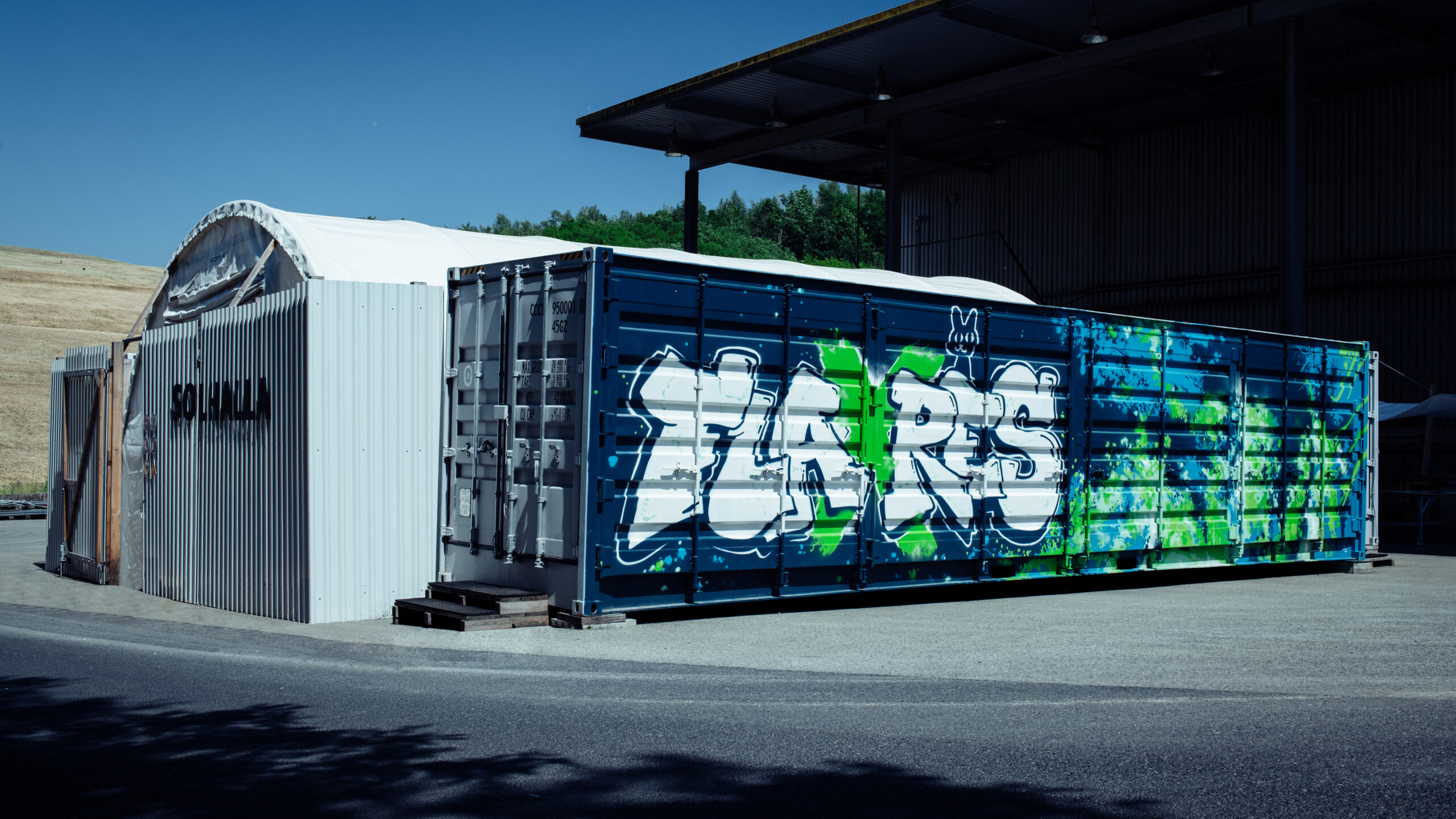